Benefits
of post-shipment inspection
PDI can provide manufacturers and suppliers with important, independent and verifiable information that helps to identify potential problems in advance and that facilitates the resolution of disputes.
Goods received by customers may not comply with all purchase requirements. Hence, they should be verified for compliance with purchase specifications, quantity, physical condition, marking & labelling etc. if the deficiency of noncompliance is not identified at the time of receipt and corrected if needed, a non-complying product may get into services leading to malfunctioning of failures. Thus, the risk of not conducting a post delivery inspection in terms of safety, economic and environmental risks can be very high. Customers often face challenges of not having adequate and qualified resources to conduct the post delivery inspections.
Our post-shipment inspection includes
Quality Assurance
The primary purpose of post-shipment inspection is to verify that the goods meet the quality standards specified by the importer/buyer. This includes checking for defects, damages, inconsistencies, and other issues that may affect the quality of the products, and any incident maybe happen during transit or at loading place or real defect from production.
Quantity Verification & Finished Goods quantity
There are three main components: Pricing Accuracy, Verifying the Net Contents of Bulk and Packaged Goods, and the Fair Packaging and Labeling Laws. An inspection reviews several important aspects of a product: workmanship, specifications, quantity, functionality, and safety. Unfortunately, limited budgets, etc.
Conformance to Specifications
The inspection at the delivery place ensures that the goods conform to the technical specifications, contractual requirements, and standards agreed upon between the buyer and the supplier.
Risk Analysis: PDI can help to importer to share actual evidence which can help for loss assessment or impose any contractual action for any disputes/rejections.
Documentation and Reporting
We provide detailed reports documenting findings, photographs, measurements, and descriptions of any defects or discrepancies observed during the post-shipment inspection. These reports serve as official records and can be used for compliance, dispute resolution, and decision-making purposes.
Here are the services we provide:
- Inspection at the receivable Port/factories/warehouse (Assessment of Operations, Assessment of Quality Standards, Tally and quantification)
- Receiving Supervision at Storage Locations (Ports, Private Warehouses, National Commodity Exchanges and Local Facilities)
- Quality Assessment at the time of receiving/post-shipment inspection (Commodity Inspection, Sampling & Testing, Tally, Condition of Goods Container, Storage Facility Suitability Assessment)
- Container/Truck Un-Loading Supervision (Bulk & Bagged Cargo)
Contact us
Why Choose
Apave India ?
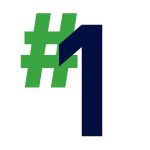
Our customer relationship approach
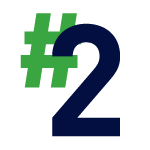
Our competitive prices
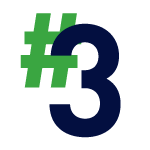