Purposes of
Non Destructive Testing
- Ensuring the Integrity and Reliability of the Product
- Preventing Accidents and Saving Lives
- Aiding in Product Design
- Controlling Manufacturing Processes
- Lowering Manufacturing Costs
- Maintaining Uniform Quality Level
No single NDT method will work for all flaw detection or measurement applications. Each of the methods has advantages and limitations when compared to other methods.
CONTACT US
Radiographic Testing (RT)
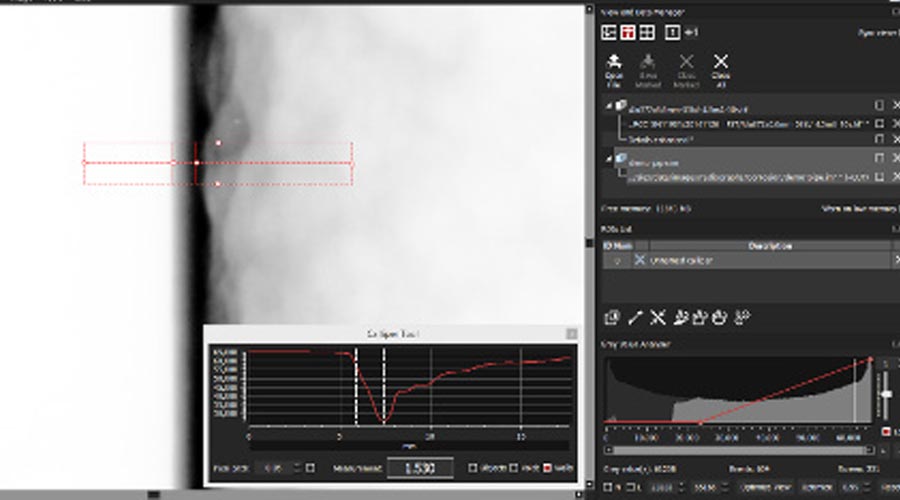
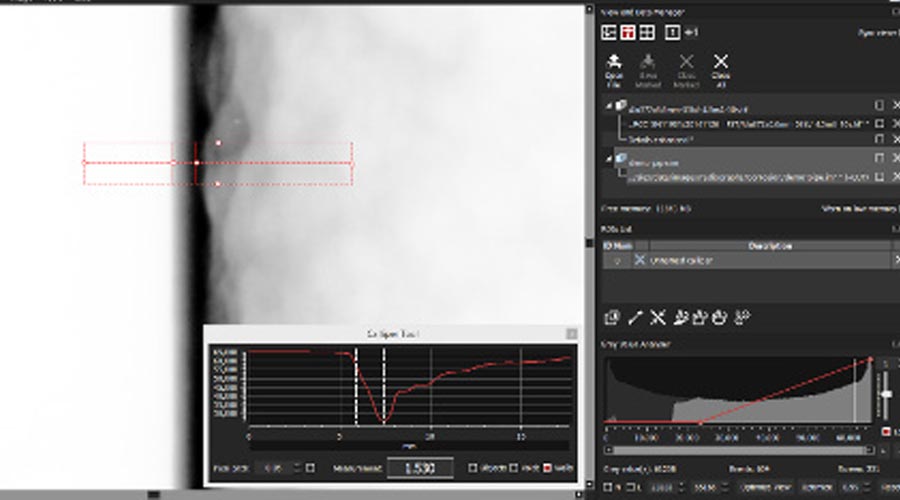
Advantages
- Can be used to inspect virtually all materials
- Most universal approach to volumetric examination
- Provides a permanent record film / digital record of the inspected test object
- Confirm the location of hidden parts in an assembly
- Detects surface and subsurface defects
- Ability to inspect complex shapes and multi-layered structures without disassembly
- Minimum part preparation is required
Limitations
- Access to both sides of the job is usually required
- Orientation of the radiation beam to non-volumetric defects is critical
- Radiation hazard to personnel
- Operating licenses are required
Film Radiography
Film and processing chemicals are used in this popular method.
Apave provides Gamma ray – (Ir-192, Co-60, & Se-75) & X-rays.
Digital Radiography (DR)
One of the biggest advantages of the use of digital radiography is its ability to significantly reduce the radiation dose in comparison to film applications. In addition, new imaging techniques have increased the capacity for visualization of defects and revealed new potential for accurate evaluation.
Computed Radiography (CR)
Computed radiography uses, flexible, photo-stimulable phosphor (PSP) plate loaded into a cassette and exposed in a manner similar to traditional film radiography. The cassette is then placed in a laser reader where it is scanned and translated into a digital image. Once digitally captured, the image may be stored on a computer or other electronic media. Archiving is made easier and the images can be electronically distributed to others for viewing.
Apave provides Computed Radiography with Ir-192, Co-60, Se-75, X-rays (CR can also be performed with SCAR/CPR system).
Small Controlled Area Radiography (SCAR) / Closed Proximity Radiography (CPR)
Objective of Small Controlled Area Radiography (SCAR) system is used in open field radiography using special projectors with Selenium 75 source and controlled beam collimators and Radshield as additional shielding mat to bring down the radiation levels below 0.2 mR/hr at 5 meters. This system is approved by competent authorities and has proven in the field beyond doubt that SCAR system can be used at construction sites without hindering contractors other work 24x7.
Apave provides Small Controlled Area Radiography (SCAR) / Close Proximity System (CPS).
Ultrasonic Testing (UT)
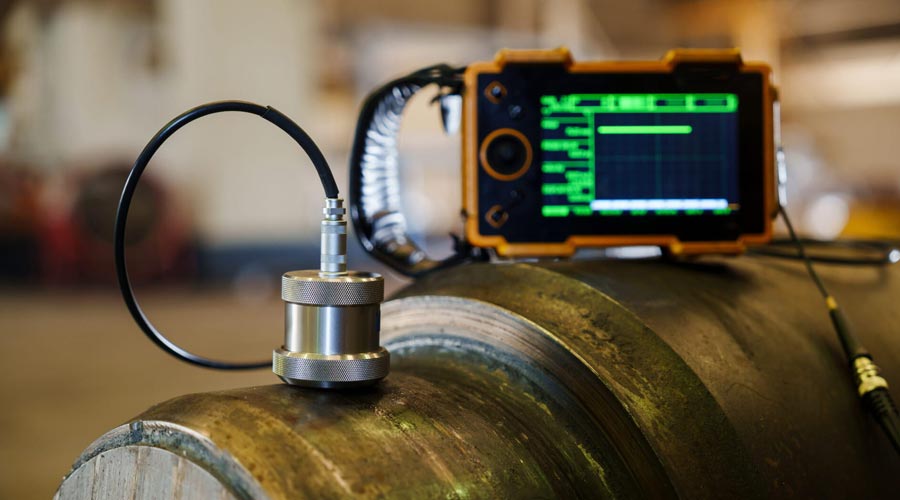
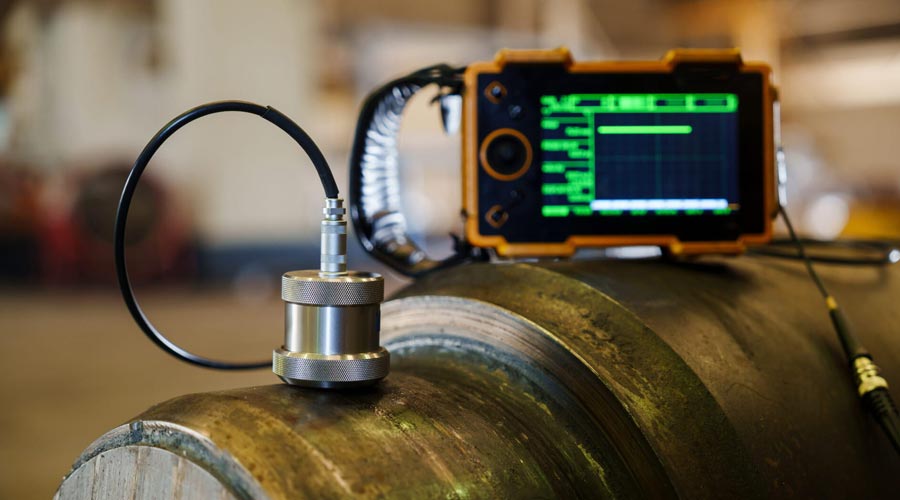
Used to locate surface and subsurface defects in metals, fabrication, steel products, plastics, wood etc. Ultrasonic inspection is also used to measure the thickness of materials and characterize properties of material based on sound velocity and attenuation measurements.
It is also used in the detection of inter laminar separations and regions that have been improperly processed or damaged in layered composite structures.
The most commonly used ultrasonic testing technique is pulse echo, whereby sound is introduced into a test object and reflections (echoes) from internal imperfections or the part's geometrical surfaces are returned to a receiver.
Advantages
- Depth of penetration for flaw detection or measurement is superior to other methods.
- In general access to only one surface is required.
- Results are generated instantly with little or no processing time.
- Highly portable equipment, which is well suited to field inspection and in-service inspection.
- Minimum part preparation is required.
- Application to a broad range of materials
- Method can be used for much more than just flaw detection.
Limitations
- Surface must be accessible to probe and Couplant.
- Skill and training required is more extensive than other technique.
- Surface finish and roughness can interfere with inspection.
- Thin parts may be difficult to inspect.
- Linear defects oriented parallel to the sound beam can go undetected.
- Reference standards are often needed.
- Less effective in highly inhomogeneous and coarse- grained materials
TOFD (Time Of Flight Diffraction)
The TOFD (Time of Flight Diffraction) technique is a computerized and automated system for weld inspection which is able to scan, store, and evaluate indications in terms of height, length, and position with a grade of accuracy never achieved by other ultrasonic techniques.
TOFD has two blind zones where it is not sensitive to defects; hence TOFD needs to be supplemented by a conventional pulse-echo examination of the near and far walls.
Phased Array UT
Phased array can successfully overcome many of the inconsistencies of the manual application. Phased array probe is constructed from a number of very small elements arranged in a line or in a specific cluster design. By activating a number of the elements at once and applying specific voltages to each element a predetermined beam angle, or beam of varying angles can be produced. Furthermore, by moving the active elements along the probe the beam is moved forward/backward in a manner similar to the movement of a manual technique.
When the phased array wedge is placed on the parent material at a specific standoff position and moved along the weld, data can be collected and imaged as a C-scan (plan view) of the weld, much like a traditional radiograph. To compliment this, the ultrasonic imaging system can also show the A-scan, B-scan (end view), D-scan (side view) and in the case of a beam with varying angles S-scan (or sectorial scan).
Apave provides:
- Flaw detection on raw materials, plates, forgings, castings.
- Weld test using longitudinal angle, creep & shear wave probes.
- UT – TOFD, PAUT.
- Thickness Measurement.
- Special probes to measure thickness on 10 mm OD tubes.
- Thickness of thin materials min 0.6 mm.
- Through paint thickness on steel measurement possible.
- Thickness measurement on hot surfaces up to 600 C.
- Bond Testing.
- UT ‘A’ scan continuous recording facility.
Magnetic Particle Testing - MT (Wet & Dry - Fluorescent & Non Fluorescent)
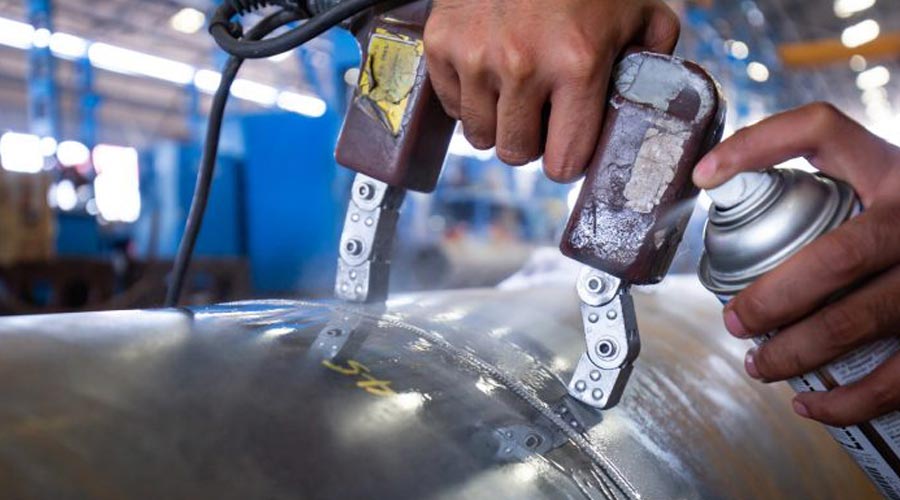
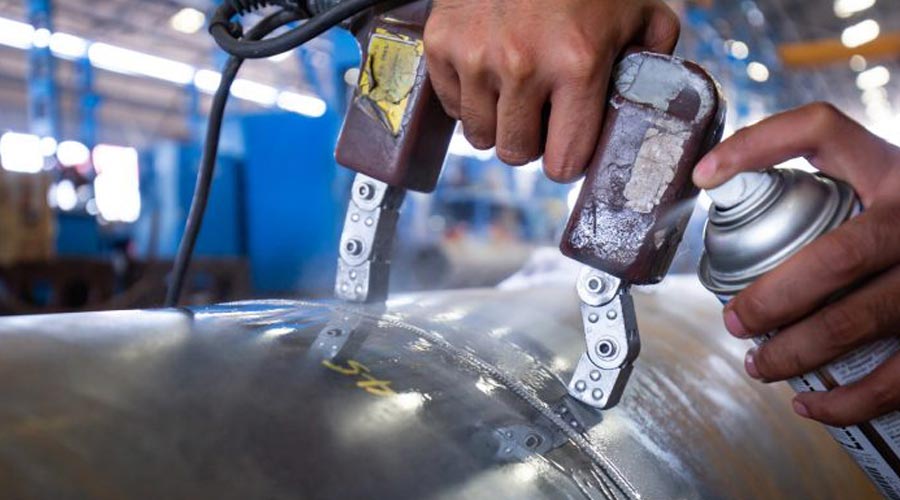
Magnetic particle testing (MT) is used to detect discontinuities in ferromagnetic parts namely parts made of iron, steel, nickel, cobalt and the alloys of these materials MT is a highly effective inspection tool that is sensitive to the presence of cracks, laps, seams and similar types of surface and near-surface discontinuities.
Apave provides:
- Prod type (Up to 8000 Amps – Coils, Central Conductor, Head shots)
- Electro Magnetic yoke
- Permanent Magnet
Advantages
- Low-cost, reliable method for locating surface cracks in ferromagnetic materials.
- Particles may be in color or made to fluoresce under ultraviolet radiation.
- Permanent magnets can be used.
- Fast and simple application process.
- In addition, the discontinuity location, orientation and approximate length are indicated on the part, making interpretation and evaluation possible.
- Visual interpretation of indications
Limitations
- Can be used only on ferromagnetic materials.
- Large electrical currents are required for certain test applications.
- Correct selection and process of application of particles can severely limit sensitivity.
- False indications often occur in transition areas.
- Burning of parts can occur at contact points.
Liquid Penetrant Testing / Dye Penetrant Testing - PT (Fluorescent & Non Fluorescent)
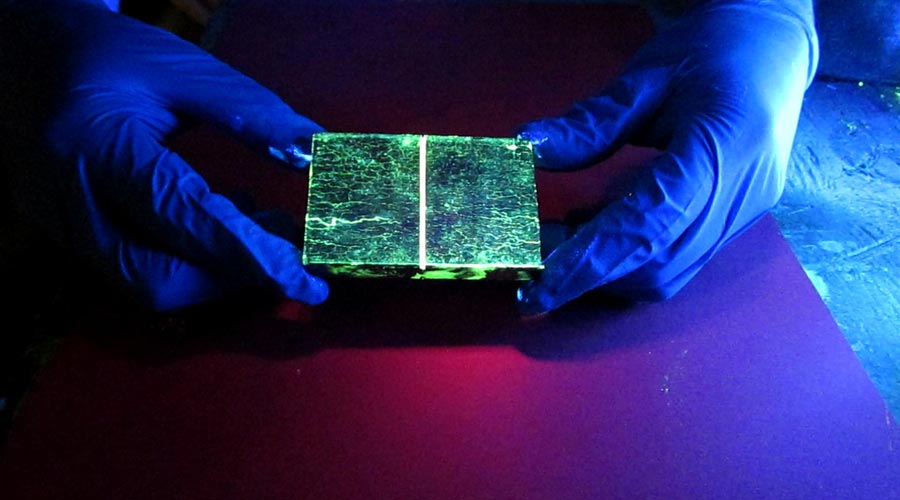
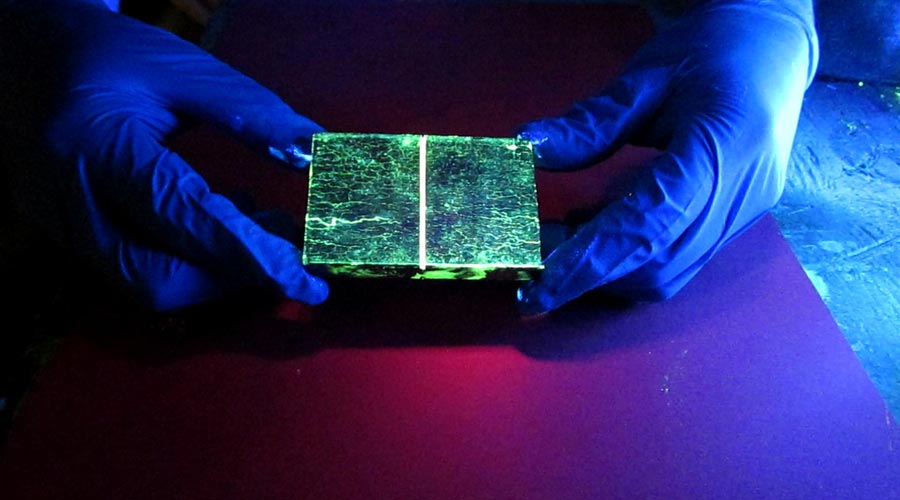
Relatively simple, inexpensive and reliable, liquid penetrant testing (PT) is used to locate cracks, porosity, and other defects that break the surface of a material.
With the correct application, it will detect discontinuities ranging in size from the large to the microscopic. Liquid penetrant testing is used to inspect large areas very efficiently and will work on most nonporous material.
Advantages
- Is one of the most sensitive NDT method for detecting very small surface discontinuities.
- Can be used on a wide variety of materials, including ferrous and nonferrous metals, alloys, powdered metal products, glass and some types of organic materials.
- Can be performed with relatively inexpensive, unsophisticated equipment.
- Is capable of examining all of the exterior surfaces of objects, even of complex shapes.
- Magnifies the apparent size of discontinuities, making the indications more visible. In addition, the discontinuity location, orientation and approximate length are indicated on the part, making interpretation and evaluation possible.
Limitations
- Discontinuities must be open to the surface, as well as free of foreign material that could restrict the entry of the penetrant into the discontinuity.
- Liquid penetrants, emulsifiers and some types of developers may cause skin irritation.
- Liquid penetrants may harm some nonmetallic materials, such as rubber and plastic. There is also the possibility of staining of porous or coated materials.
- Some liquid penetrant materials contain volatile solvents thus, adequate ventilation is necessary, especially in confined areas.
- Liquid penetrants, especially in aerosol form, are flammable. Inspectors must follow manufacture's recommendations regarding necessary personnel protective equipment when using such equipment.
Leak Tests (LT)
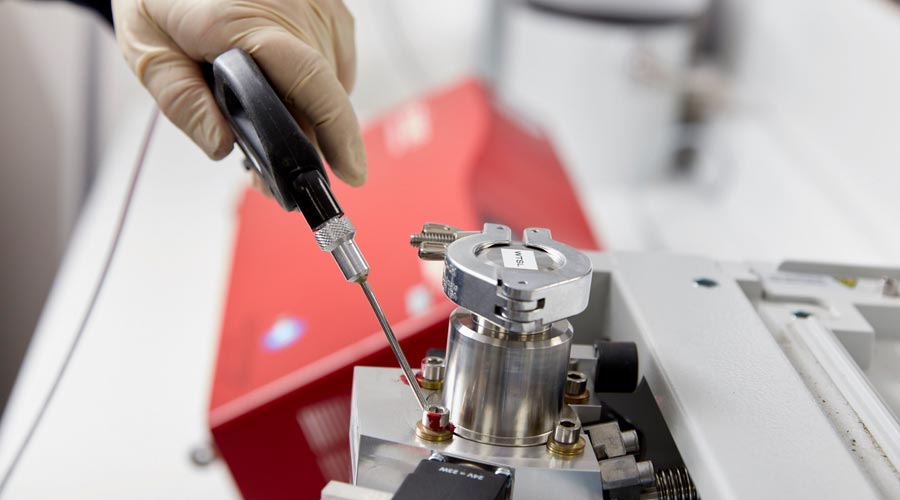
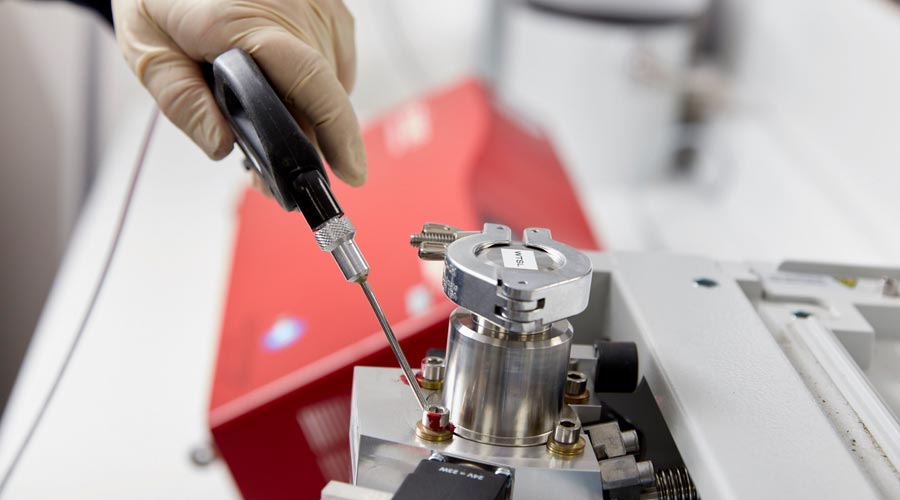
Apave provides:
- Helium leak detection – Mass spectrometer
- Detectable leak rate - Pressure vacuum 10-2 to 10-11 cc/sec.
- Detectable leak rate - Vacuum method 10-4 to 10-10 cc/sec.
- Detectable leak rate - Pressure method 10-1 to 10-7 cc/sec.
- Ultrasonic Leak Detection to detect gross leak from the system
- Detectable leak rate 10-1 to 10-2 cc/sec.
- Vacuum Leak Detection for tank bottom plates etc
- Detectable leak rate 10-1 to 10-3 cc/sec.
- Halogen Leak detection to locate gross leaks
- Detectable leak rate 10-1 to 10-8 cc/sec.
- Pneumatic leak detection to test pressure leaks
Hardness Testing
Hardness is the property of a material that enables it to resist plastic deformation, usually by penetration.
However, the term hardness may also refer to resistance to bending, scratching, abrasion or cutting.
It is essential to evaluate the value of the hardness of welding and other materials to understand their usefulness in the process.
We have a non-indenting type tool which gives very accurate reading in any position. We also measure hardness of non-ferrous and rubber parts.
Apave provides:
- Poldy Hardness Measurement for Metals
- Non indenting type Hardness Measurement for Metals
- Hardness Measurement of Rubber
Ferrite testing
Apave provides Ferrite testing due to its Austenitic & Duplex materials.
Visual Testing (VT)
The most basic NDT method is visual examination, one of the best tool used in manufacturing process to identify surface defects / imperfections on the spot assisted by devices that magnify, qualify or quantify the conditions being evaluated.
Inaccessible areas of parts can be inspected using remote visual examination method. In this flexible fibroscope or boroscope is used with xenon lamp to view internals of the part and can be video graphed. Measurements of the flaw can also be easily done.
Most NDT inspections start with a visual inspection.
Positive Material Identification (PMI)
Portable XRF Spectrometry system can quickly and easily identify material composition and quantify elements in parts or test samples without the need for wet chemistry or destructive testing.
P.M.I. provides chemical analysis and material grade identification for most alloys, metal powders, sintered alloys, metallic coatings, and precious metals.
The versatile, handheld, rapid analyzer employs multiple calibration and testing options with a built-in data library for on-the-spot, accurate material matching, identification, and analysis.
Other testing
Repair & Servicing of NDT Equipments
Servicing & Maintenance of NDT Instruments is an important aspect for the success of NDT operations.
It is quite unusual for an equipment to be used consistently without needing repair. Malfunction includes equipment not operating in a safe manner, not operating at all, not functioning normally. We repair properly and on timely basis.
It is essential in the NDT operations to complete the expected output within time schedule. This is possible. If all equipment’s are timely serviced & maintained in systematic manner including calibrations, operation becomes effective.
We also offer preventative maintenance contracts to ensure a customer’s equipment is both calibrated and operating at peak performance.
NDT Training & Consultancy
Success of NDT results is largely depends upon training, qualification & experience of NDT personnel. We train internal & external candidates on various mock-ups for hands on experience in performing NDT and interpretation of results.
We also provide NDT consultancy in establishing system and procedures for NDT.
Our facilities include :
- Reference books in NDT & material processing
- National & International NDT codes & specifications
- Reference Radiographs
- Sufficient Calibration Blocks & Reference Blocks
- Sufficient NDT specimens with covered defects in various configurations for practice
- Radiography Enclosure with darkroom
- Customer specific training
We provide :
- NDT training & Certification to ASNT Level I & II in RT, UT, MT & PT
- ASNT Lv. III services for Inspection & Consultancy in NDT
Why Choose
Apave India ?
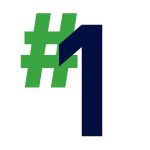
Our customer relationship approach
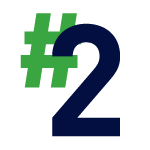
Our competitive prices
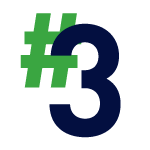